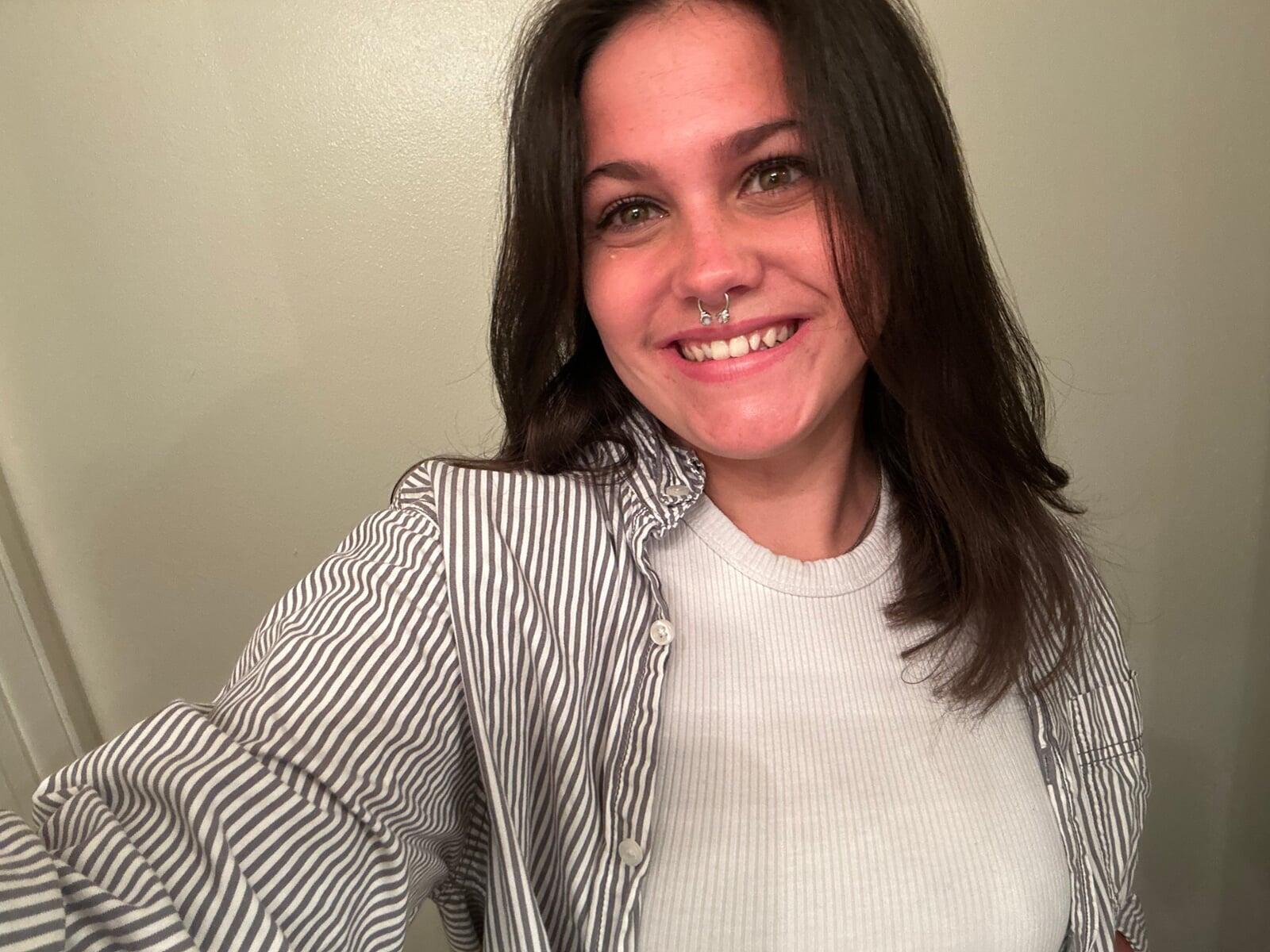
Samantha Donoghue
2025 Intern
I am writing to share my experience and express my gratitude for the opportunity to work in a hands-on horticulture and retail environment over the past several months. This role gave me valuable insights into the plant industry and helped shape my future career goals.
From January through February, I gained foundational experience in greenhouse operations. I learned to stick cuttings, organize plant tags, and build designed plant containers. I also helped with inventory by counting seed and young plant plugs. Through daily operations, I observed how the company addresses common challenges, such as late truck deliveries or damaged products, and how overflow inventory is utilized to fulfill backorders efficiently and professionally.
In March, I learned how to organize plants on shipping racks, scan inventory for accuracy, and water plants on a large scale. I developed an understanding of plant health by learning how to identify signs of under- and overwatering, and how overwatering can lead to pests like fungus gnats.
By April and May, I took on a supervisory role, managing three teams and working directly with Costco managers to ensure high standards were met. I gained experience in merchandising plant material to maximize sales, resolving staffing issues, covering shifts, and organizing schedules to keep team productivity high. Supporting my team and maintaining a positive working environment became one of my key priorities. In June, I visited garden centers and learned how they structure teams to care for plants and assist customers. I saw unique customer-focused programs, including container plant orders and in-house landscaping services, designed to reduce customer stress. I was also introduced to the basics of HR and IT, including seasonal staffing costs, payroll, and handling internal issues.
My experience with Tagawa Greenhouse was truly impactful. As a host company, they offered valuable opportunities to explore nearly every department within their wholesale production operation. I was also able to gain firsthand experience in both large-scale and small-scale retail environments. This well-rounded exposure not only gave me a deeper understanding of the horticulture industry but also supported my personal and professional growth. Tagawa’s commitment to hands-on learning created an environment of continuous development and gave me the confidence to take on new challenges.
My experience with Tagawa Greenhouse has strengthened my leadership, communication, and organizational skills. It has confirmed my passion for working with plants, and I am excited to continue exploring plant care and design, especially the creative container displays I saw in the garden center. Additionally, my time supervising teams in April and May sparked a strong interest in leadership, and I plan to pursue more opportunities in supervisory or management positions within the horticulture industry. I look forward to building a career that blends both the artistic and operational aspects of plant work.
I am truly thankful for the opportunity to work with Tagawa Greenhouse. The experience met both my personal and professional goals, and I’m grateful to have been welcomed into such a dynamic work environment. Learning about new plants, techniques, and responsibilities has made this a meaningful and unforgettable part of my journey.
I am also sincerely grateful to the Vic & Margaret Ball Internship Program for making this opportunity possible and for providing guidance and support along the way. Being part of this program has played a major role in my growth and career development.
— Samantha Donoghue
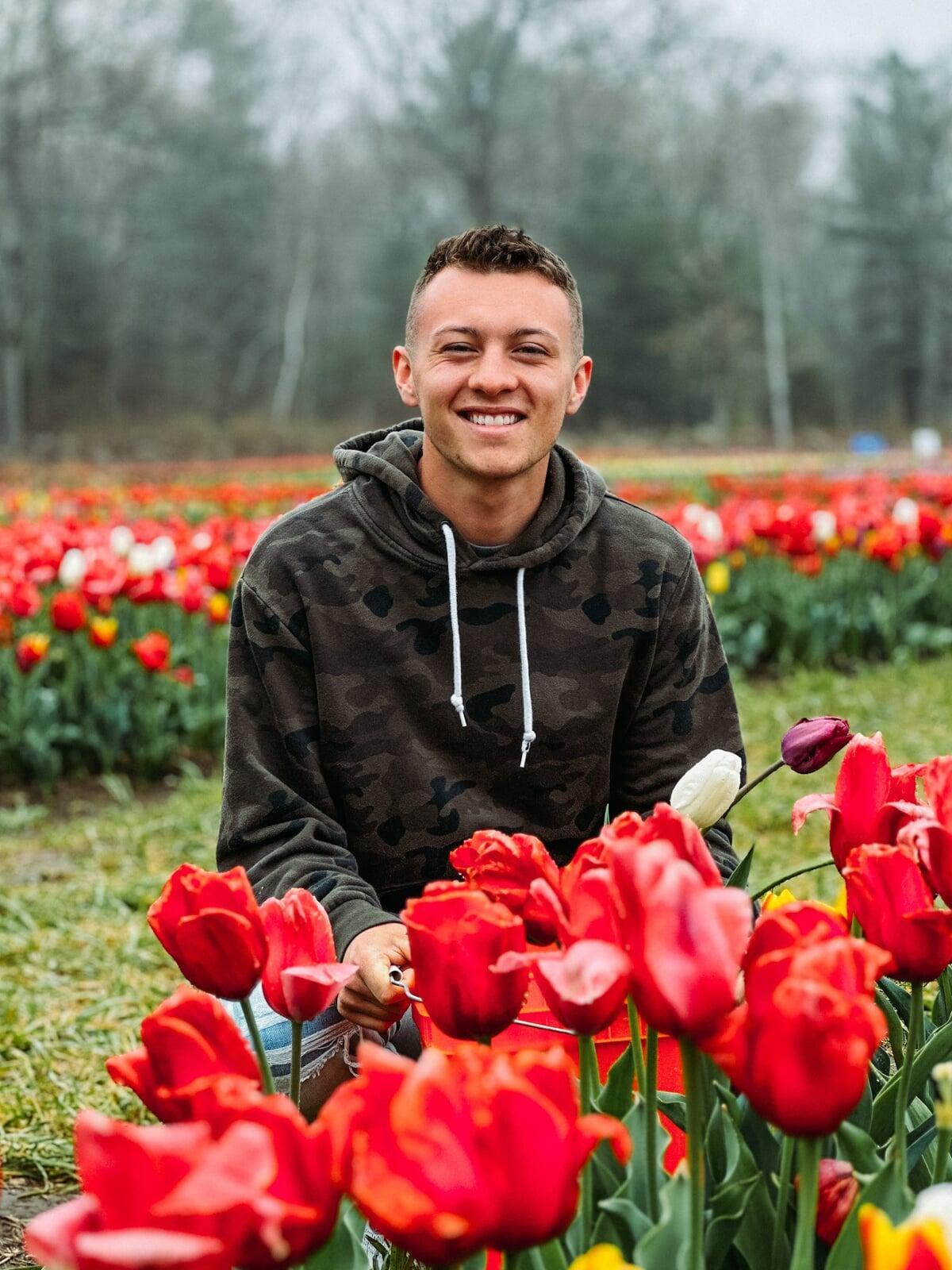
Joshua Dick
2024 Intern
★ 2025 Paul Thomas Intern of Year
My six-month internship experience with Tagawa Greenhouse Enterprises has been truly a life-changing experience for me, and one of the best decisions I have made. I have experienced so many different aspects of the horticulture industry, but also other opportunities I did not realize would be extremely beneficial.
To start off on the experiences I’ve had, this internship was broken up into different rotations. The first rotation was seven weeks long from the beginning of January to the end of February at one of the growing locations. This greenhouse was located in Golden, CO right at the base of the foothills. The primary focus at this location was growing unrooted cuttings for plug trays in their ‘young plants’ program. This is one of the two main products that Tagawa produces. A typical work week would consist of unboxing cuttings that came from different growers and organizing them into large coolers.
The cuttings would sit in these coolers until they were ready to be ‘stuck’ into trays. They had a ‘sticking line’ set up to take the bags of cuttings, give them to a worker to stick into the trays, and then go out to the greenhouses where they would be set up on a schedule to be misted until they are rooted in. There were three types of trays they would use, a 50 count, 102 count, and 200 count. Some plants had two cuttings per tray, most had one. The 200 trays were prefilled with media, but the 50 and 102 counts had a machine that would make ‘ellepots’ consisting of soil wrapped around a biodegradable substance.
Most of the trays were stuck by hand, but Tagawa also has an AutoStix machine, which requires a few people to run the machine. Lines of cuttings with biodegradable plastic holders would be fed into the machine, and an arm would grab them to stick into trays. This was fascinating to watch the process!
Another job that me and the other intern Tate Erickson did was to go through the list of trays that would be shipped out for the next week and ensure that there were enough trays to ship. If there were any issues (not good rooting, too small, poor quality, etc…) then we would make note of that and a decision would be made to address the issue. For the plants that we're shipping out that week, we would place a ‘jimmy tag’ on the tray for them to be picked up. These tags would be printed and a team would go out to find the trays. The tags had a location that showed which range (greenhouses 1-5), north or south (each greenhouse has a center aisle to look at the north or south side), bench number, and letter. This gave a pretty specific location to find the plants. Throughout the entire process at Golden, one of the main skills I learned was plant identification, as it was crucial for unboxing, sticking, and especially finding the rooted trays for orders. I also had a chance to learn and work on my Spanish since most of the employees I worked with here were part of the H-2A program and many of them did not speak much English. This is very apparent in the horticulture industry, and I would like to continue learning the language!
The next seven weeks were spent at the main location, which includes many acres of greenhouse space, as well as the main offices in Brighton CO. The first three weeks I spent irrigating with Javier in range 3. We mainly grew petunia plugs trays. These were seed grown petunias that were in various sizes of trays such as 128, 288, 324-punchable, and 512. I spent the next 2 weeks with Manuel in range 1, where I got to see how different growers/irrigators will treat the same product differently, and it makes for a much different outcome. The more plants are stressed and dried down, the deeper their roots grow, and the less they will swirl in the trays. This makes for stronger and more resilient plants overall. Although I did not apply any pesticides or plant growth regulators (PGR’s), I talked with the growers about the products they use for pesticides and PGRs and how important they are when aiming towards a certain goal. This is especially the case for finished products like the Costco/InColor program. At this time I also got the chance to understand how a boom irrigator works, and how essential it is when constantly watering millions of plants every day.
The last two weeks at Brighton I was able to get exposure to a little bit of all the other stages of Tagawa’s Power Starts program. I seeded many of the trays, which is done with a vacuum seeder. The seeds are put into the machine, and suction pulls them into the right place so they fall into the cells. I helped to transplant trays, which means to make full, healthy trays and remove any cells where seeds did not germinate. Most of the trays at Brighton are started from seed, and Tagawa has high standards for order fill with trays. We used snail forks to dig out and transplant, but there is also a machine that will blow out the empty cells and replace them so the process is somewhat automated.
I had some time to work in the collation area, which is packaging up the trays to get ready to ship. Many of the trays go into boxes that have cardboard inserts that make shelves so the plants do not get crushed. Others will be shipped out on racks, but the difference is up to the customer. The last section I went through was shipping. I put together several CC racks for shipping many of the plants out for Costco. The boxes of plants would be stacked onto pallets and wrapped in plastic to hold them together. I had the opportunity to learn how the semi trucks were packed, and actually created layouts for the trucks going out. They would use straps, bars, and need the weight to be evenly distributed across the truck.
The next seven weeks were much different than I was expecting, but overall a great experience. We started the Costco/InColor rotation, which focuses on the other side of Tagawa’s business. Besides shipping out young plants to garden centers and other growers, Tagawa also grows finished products that are shipped to Costco warehouses all throughout Colorado. I was actually promoted to a supervisor for two of the busier stores in the program. One was in SW Denver (Littleton) and the other in Sheridan. My roles included creating schedules for all of my sales associates to ensure there were people there to unload new deliveries, water and care for plants, and merchandise. With each order came a BOL, or Bill of Lading. We also had damaged or poor products that would come up, which we would need to RTV (which stands for ‘Return to Vendor’.) I would submit all of this paperwork through an app that all supervisors, managers, and others could view to ensure that the stores were functioning as needed. I also ensured that being a guest at Costco, we would follow their expectations and keep our set looking clean and organized. We also got reports for sales, and I was able to get a good idea of how well each store was doing, what products sold well, and what we could do to increase sales. I learned a lot about supervising other employees, such as learning how to talk to people in a more professional way, dealing with conflict, and learning independence with a schedule to ensure all work is completed. I was not scheduled for any specific times during the day or week, so it was my job to ensure the stores were in functioning order, and that gave me a whole new set of skills I had never been challenged with before. While I was at Costco, I also gained a lot of knowledge and skills on what plants sell better and why, and how to merchandise a whole new set of products.
The next rotation was pretty short as we were running out of time for the internship, and the Costco InColor rotation lasted a bit longer than expected. We spent four days at Tagawa Gardens, which is the retail garden center in Centennial, CO.
Since we had limited time, we spent some time in each department to learn how each area functions and met some of the employees. During this week, there was a large tree shipment that came in, so we helped out quite a bit with unloading that truck, and moving the trees to the areas in the lot to be sold.
The departments we worked through were: nursery, perennials, annuals, production, cashier, front office, and getting an overall tour with Chuck. The garden center had slowed down a lot that week after the spring rush was over and it was starting to get warm.
The final rotation was the Business and Administration rotation. This consisted of sitting down with multiple people throughout the offices in Brighton and discussing what their job is and how it ties into the process of the company. Many of these people have the ‘behind-the-scenes’ positions that you may not immediately think of. A great example are the three women who make up the distribution team. They work to put shipping routes together throughout the country for young plants, as well as the Costco locations throughout Colorado. We also got a chance to tour the Colorado State University trial gardens up in Fort Collins and the Denver Botanic Gardens.
Overall, I have learned a tremendous amount of knowledge and information that I can take with me throughout my career in horticulture. I am extremely grateful for having this opportunity through Tagawa Greenhouse Enterprises, and to see all different facets of a large plant production company. Through my experiences and rotations I have learned that my interest in horticulture has started to shift into two different potential paths for the future. Before the internship started I worked at a family owned garden center, and taking that experience along with the rotation at Tagawa Gardens, I do have an interest in the garden center industry. Whether that could mean working for a larger garden center like Tagawa Gardens, or owning my own place someday, it is quite intriguing. I also have taken quite an interest in horticultural marketing, especially after the Costco/InColor rotation, and how to develop products that follow the current trends and keep people interested in plants. I was also inspired to take a “Marketing Principles’ class in the fall at my university so I can tie that into what I have learned with my internship. In the end, these six months have been truly eye opening for me, got me out of my comfort zone, and helped me understand myself in terms of career advances, and overall life decisions. This was an incredible experience for me and if I could do it again I certainly would.
— Joshua Dick
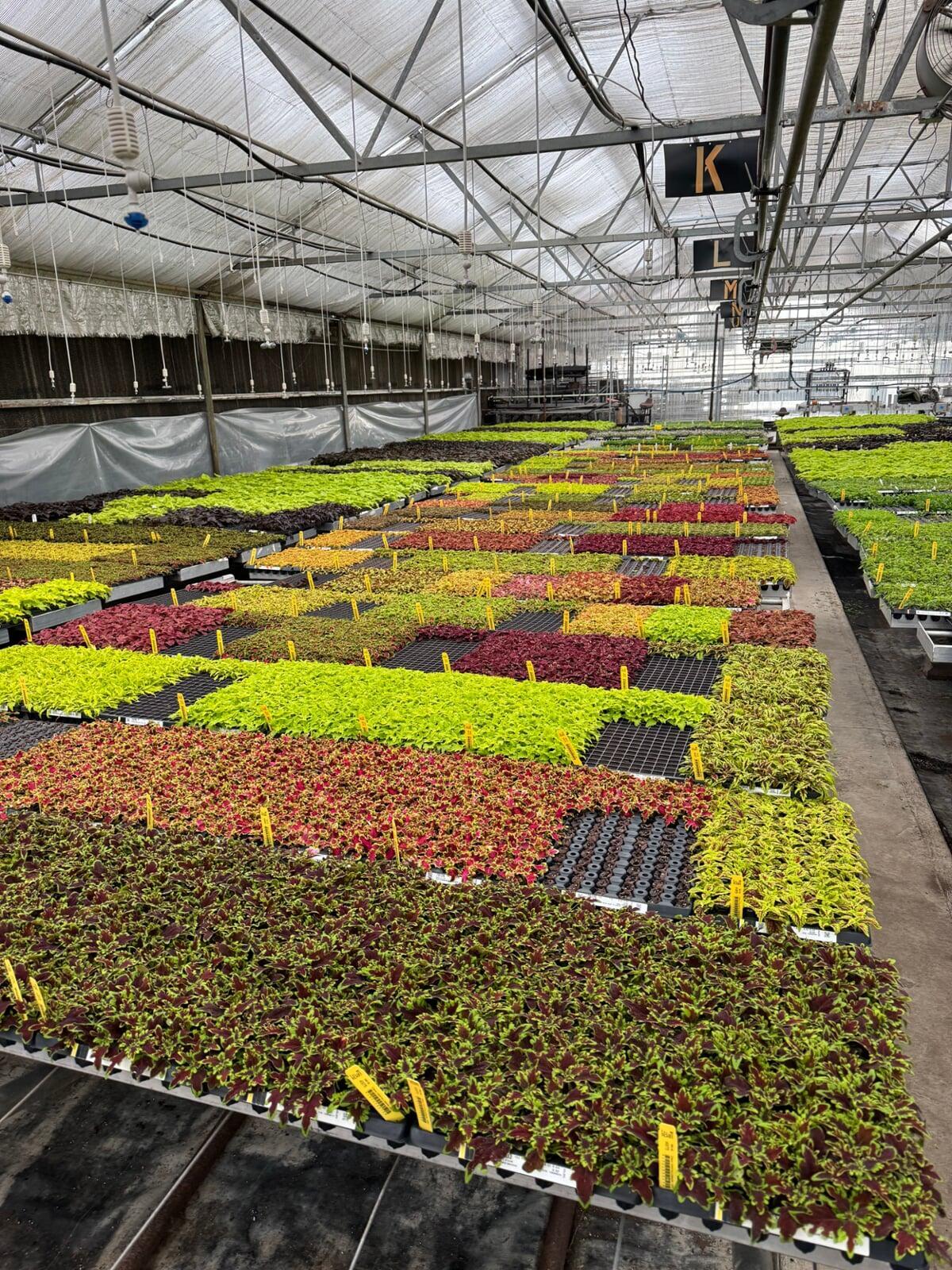
Stephen Burn
2024 Intern
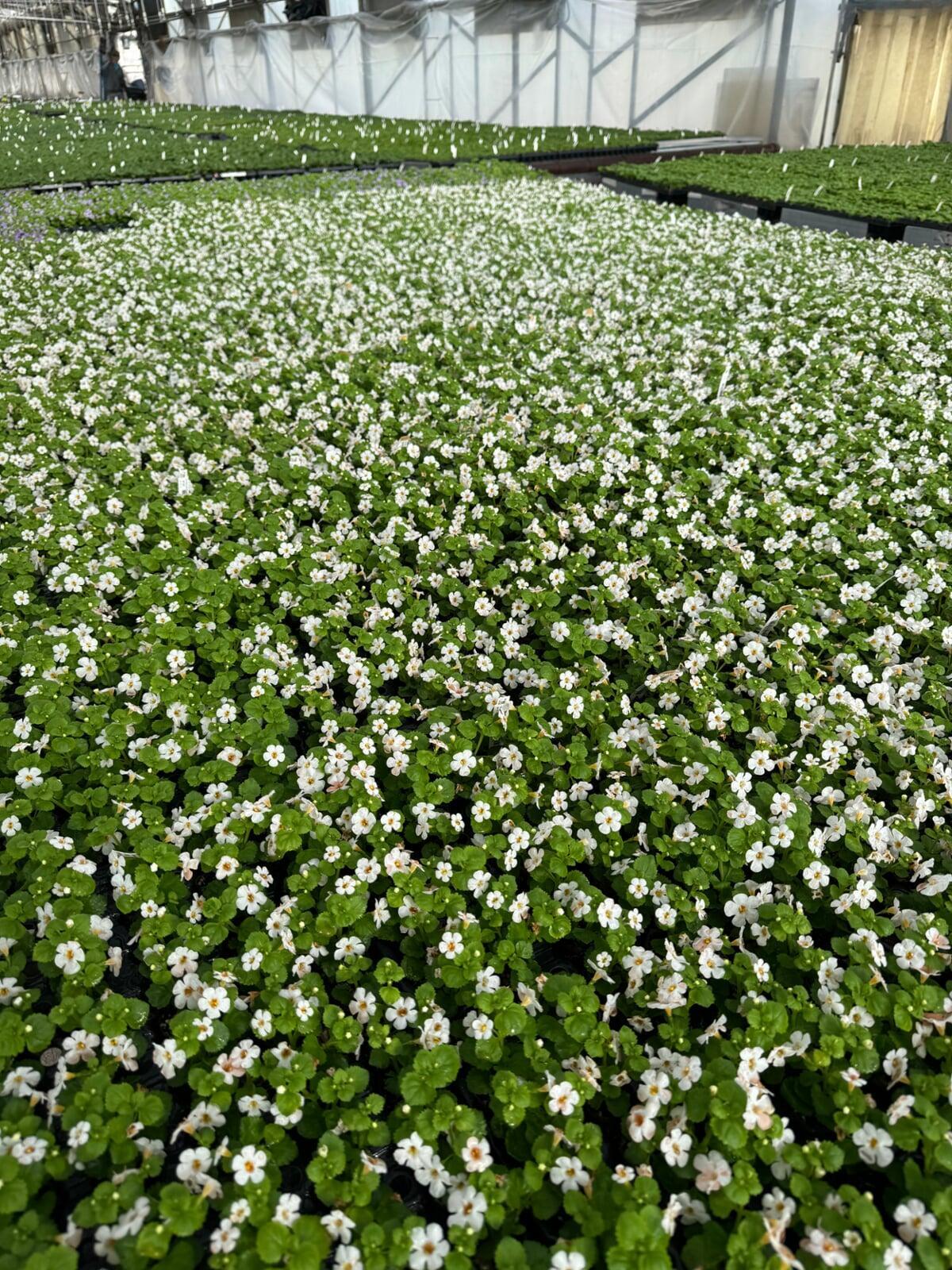
Rykar Kimura
2024 Intern
Throughout the internship program with Tagawa Greenhouse, I have had the opportunity to experience and learn about all aspects of the business including operations, production, retail, and business and administration. My scope of horticultural knowledge has broadened and I can already envision the ways this will help me both in the workplace and in life. At the beginning of the internship, I was taught about the importance of lean, minimizing waste, and increasing efficiency. This framework gave me the proper mindset needed to navigate the next six months of the internship.
Starting with operations, I was introduced to the seeding area in Brighton. Here, we fed trays onto conveyer belts, assisted in hand-seeding, ensured the soil structure and moisture levels were up to standard, and sorted finished trays on carts to be taken to the germination chambers. The seeding lines were very fast-paced and required me to plan my next steps whether it was running to get plastic covers for trays, fill up soil, prepare a new cart, or run over to the line next to me to do the same tasks. The job seemed overwhelming at times, but I came to realize that the machine wasn’t going too fast, rather I was going too slow. My quick thinking skills were tested which has helped me remain calm while stressed which is important in an industry as intense and volatile as horticulture. The seeding manager frequently walked around the various lines to check their quality and observing this gave me a better idea of how to do quality control without micromanaging. Finding this balance has been difficult for me in the past, but now I feel like I can handle these situations when they arise.
We then spent time in the seed inventory mainly doing receiving and storage. We were shown how and when to order more seeds when the stock was low which helped me get a better understanding of supply chains, safety stock, and lead times. The biggest learning curve was the AS/400 computer software. Despite being outdated, I became grateful for learning how to use the software months later after learning that other companies like Costco also used it. Although I did not see other parts of the Brighton greenhouse during this rotation, I am appreciative of the relationships I made with the other seeders even though we didn’t speak the same language.
Next was the production rotation in Golden. During this time, I helped with verifying tray counts, grading, pinching plants, jimmy tagging, and documenting spray records. I learned a lot about the importance of organizing a greenhouse. With so many moving trays, it was sometimes a challenge to find where the plants were that we needed to do record keeping for especially if the new locations of plants were not entered into the system.
Once production slowed down, we helped Tagawa’s InColor team at Costco. My favorite part of the job was setting up the flower displays before opening because each day was like solving a new puzzle depending on what products we had or what we wanted to promote. After opening, we consolidated and removed racks, kept the floors clean, and watered plants. One store I worked at consistently had more racks delivered than the store was able to take. Communication was therefore a large aspect of this rotation. I often found myself coordinating with Costco’s receiving department and general manager to plan a smooth delivery to get our plants from the back of receiving to the front of the vestibule. Furthermore, several of my coworkers would come to me for instructions when our supervisor was away which I was not always prepared for. However, this helped me prioritize tasks and delegate them to the people I worked with. I am not one to tell others what to do, but I feel much better giving instructions to coworkers.
The next rotation took place at Tagawa Gardens. At the garden center, we helped out the nursery with a delivery and cleaned the annuals section. We also had the opportunity to talk to several department managers including the front office, cashiering, production, and events. It was very valuable to hear everyone’s insights and learn their thought processes when doing their job. For example, the lead cashier mentioned how she more than tripled the sales of gloves by asking to change how they were displayed. I wasn’t expecting much from cashiering, but she made it sound a lot more interesting than I would have expected. This drove Tagawa’s philosophy of always looking for improvement further into my mindset regardless of what job I may be performing.
The final rotation focused on the business and administration departments of Tagawa Greenhouse. We talked to managers from HR, finance, IT, InColor, young plant production, and maintenance. These deep dive conversations opened my eyes up to several aspects of jobs that I otherwise did not consider. I learned that HR is responsible for a lot of the strategic management which serves to establish a culture within the company that makes workers more engaged and willing to support the company’s goals. Because the IT department can oftentimes get overlooked in a greenhouse business, I was taught the importance of being on the ground and trying to connect with others. Seeing the Excel sheets that the finance department creates showed me the consideration required when calculating every potential expense and earning. I found it amazing that each plant sold from Tagawa could be priced down to the penny and then the expected revenues could be projected within minimal deviation. I also got a grasp for how to use and communicate these numbers when trying to sell a product or negotiate with a company such as Costco. On the last day, we talked to several other departments including procurement, distribution, marketing, inventory, and maintenance. It was interesting to learn about each of these functions, and it helped piece together all of the elements that make the company run. We also got some insight into the horticulture industry as a whole and current trends that each team was observing. Each conversation was very helpful for getting a better understanding of all the jobs going on behind the scenes in the greenhouse that give Tagawa the ability to operate each year.
There were some aspects of the internship that I wish were different. I spent all seven weeks of the first rotation only in the seeding area. When the other interns did their rotation, they were able to spend time in various areas across the facility, giving them more exposure to all the processes in Tagawa’s main facility. I also wish I had more opportunities to talk to the managers I worked with during the operations and production rotations so that I could better understand their roles and thought processes when growing. However, I understand this is difficult to accomplish during peak season.
Overall, I am extremely grateful that I had the chance to partake in such an amazing program with the other interns. We all learned a lot from Tagawa as well as each other. There was so much new information to take in, and I do feel like I absorbed a good amount of it. My horticultural knowledge has definitely expanded, and my skills are more well-rounded now. This internship is a formative seed in my horticultural career, and I am confident that I will use this experience to further help me grow.
— Rykar Kimura
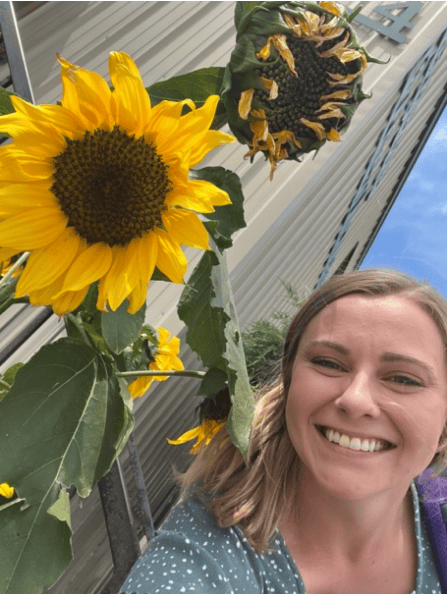
Megan Nelson
2023 Intern
★ 2024 Paul Thomas Intern of Year
My internship with Tagawa Greenhouses through the Vic and Margaret Ball Intern Scholarship Program has been an emboldening experience and a true blessing. I spent six months living in the beautiful state of Colorado and working for one of Greenhouse Grower’s ‘Top 100 Growers’ that grows “Amazing Plants, Extraordinary People, and Relationships that Last.” Tagawa puts forward a well-rounded and thought-out internship opportunity that has allowed me to see the inner workings of their entire operation from beginning to end including seeding, Auto-Stix’s processes, growth, distribution, merchandising, retail, and administration.
I started my journey at the Headquarters location in Brighton, Colorado, where I learned the history of Tagawa as a family-owned and operated business along with the other leadership and facilities that make Tagawa, Tagawa. I then jumped into seeding, where you worked fast, and the days went faster. My favorite part was racing against time to ensure there was only one marigold seed in each cell before it got out of reach.
The following rotation moved me to Arvada, Colorado where I joined the team at the Foothills facility. Here I completed my operations rotation unpacking Auto-Stix boxes and working with the machines, joining URC hand-sticking lines, Jimmy Tagging outgoing orders, and helping movement teams with outgoing and incoming products. Working with the Auto-Stix machine was my favorite part, as we only get to see videos of them in our classes. Getting to work with one was outstanding.
Remaining at the Foothills facility, I began my production rotation fulfilling pre-finished orders (filling missed pots, correcting mistakes, and taking inventory and location notes). It was encouraging to be trusted with the attention to detail needed for keeping the gold standard that Tagawa customers expect and deserve. I enjoyed the Foothills facility the most. All of Tagawa’s employees are lovely; however, Foothills was especially welcoming. Everyone was friendly and made me feel at home.
My production rotation then moved back to Brighton. Their new Piccadilly facility needed extra hands, and mine were happy to help. Piccadilly was acquired to keep up with the high demand from customers like Costco and Home Depot. Products produced here were mostly the more significant “combination” planters and hanging baskets that were being placed on a drip irrigation system. However, until the irrigation systems were in place, we hand watered. Watering took up much of the time in the first several days. Soon, I was given other tasks like scouting for pests and diseases, assisting with pesticide sprays, learning and troubleshooting the Galcon irrigation systems, joining the crop walks with other growers, and replenishing my fertilizer tanks.
I learned so much at this facility. The two biggest takeaways were disease scouting and the environmental control system of Galcon. As this was a somewhat new facility to Tagawa, there were some kinks to work out, with the main one being Galcon, as they primarily use Argus irrigation systems at the other facilities. My mentors taught me what they knew, and then I was able to explore and learn the systems to the best of my abilities. Soon, one of my mentors le_, and I became the point person for the growers, changing temperature and shade cloth settings, doing constant checks on the systems, and trying to solve any issues before taking them to the assigned Galcon technician. I also very much enjoyed attending the crop walks. I learned so much as the growers discussed what they were doing and why. My production rotation was extended by two weeks so that I could help train their new scouter. This new position was created to support growers and keep on top of any pest or disease issues. I was delighted to be given this opportunity and enjoyed sharing and expanding my skills.
The merchandising and retail rotations were exciting as horticulture retail was my first job, and I had not been back in that atmosphere since 2019. I spent a week at Costco and Home Depot, which were surprisingly very different. At Costco, our top priorities were consolidation, watering, customer service, and cleaning. Our goal was to empty as many racks as we could each day and keep the floor swept. We were also tasked to be the “food samplers” for plants, constantly checking in with customers, asking if they needed help or had questions. Home Depot was very different because we prioritized keeping the product stocked and displayed nicely. I was able to fill the role of acting as Field Manager as they were short one this season. I visited anywhere from one to four stores daily, supporting the InColor staff, stocking displays, or making new ones depending on what sales were going on that week. Getting creative with displays, working with customers again, and getting the opportunity to fill an important role made this rotation very fulfilling.
The administration rotation took me back to Brighton at the Headquarters facility and helped me to understand all the work that goes into planning and managing a season from purchasing and space planning to distribution processes. I had the pleasure of sitting down with almost every department to learn the crucial parts they play in a successful season. This rotation was a great exposure for the position I had accepted back in Kansas just days prior, where purchasing would be one of my greater responsibilities. This rotation helped explain all the roles outside the greenhouse to give me that last piece of the puzzle.
I value my education deeply. I value my professors and classmates, who are always eager to learn. However, some things cannot be taught in the classroom for a hands-on learner like me. For example, our teaching greenhouses are a li\le too small for an irrigation boom. At Tagawa, they have one in every house, and they showed me how to operate it and let me run booms for a day. Experience goes a long way in our field, and I am very fortunate to have participated in programs that value education and experience.
Tagawa has been a godsend. They provided housing for my entre internship and were with me every step of the way. They even took me to the CSU Trial Gardens and the Denver Botanical Gardens at the end of my internship. I am grateful for my time with Tagawa and recommend this internship to others looking for a complete greenhouse internship. As far as my future, I have one year le_ at Kansas State University, where I will finish my Horticulture Production degree and my Natural Resources and Environmental Sciences secondary degree. During my final year, I will also be assistant teaching for the Greenhouse Management course, fulfilling my duties as Horticulture Club President and Poinsettia Sales Co-Chair, working in the Kansas State University Horticulture Greenhouses and training for my new job at Kaw Valley Greenhouses, where I will transition to full-time after graduation. I would like to thank Tagawa Greenhouses and the Vic and Margaret Ball Scholarship Program for giving me the opportunity to learn and grow in my academic journey.
— Megan Nelson
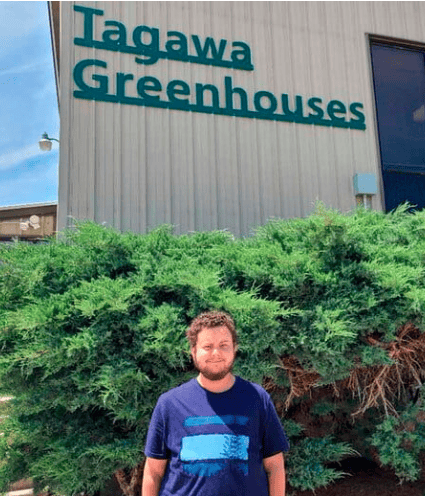
Will Billmeyer
2021 Intern
★ 2022 Paul Thomas Intern of Year
My time at Tagawa Greenhouse was an invaluable part of my education. During my six-month internship, not only was I able to apply all that I had learned from my degree program, but learned just as much, if not more, than I had in the classroom alone. Although my education had well-prepared me for a career in the horticulture industry, there truly is nothing like hands on experience in the field.
At first, I was hesitant to move halfway across the country for an internship, but I was surprised to by how much knowledge I gained from the location alone, Colorado having unique microclimates, multiple hardiness zones, and unique issues related to elevation that gave me a chance to learn about different natural ecosystems and sustainability practices.
The first four months of my internship was spent in production of young plants at the main facility in Brighton, Colorado, where I started in seeding and was able to witness the progression of the crops until they were shipped out. The majority of my time was spent under one of their head growers that oversaw germinating seedlings. From her, I learned much about the differing cultural needs of various annuals. Through both experience and detailed explanation of why we perform specific tasks, I was able to learn about irrigation, plant growth regulators, and environmental controls within a large-scale greenhouse.
In a range full of stock plants, I got hands-on experience identifying common greenhouse pests and diseases, applying biologicals, properly pruning herbaceous plants, and testing soil EC and pH. My classes had prepared me somewhat for these tasks, but I was grateful to be able to apply this knowledge in the field. Although I was unable to visit the facility where most cutting and sticking of plants occurred due to Covid-19 restrictions, I did get to spend time in the stock range and watch the cutting process on a much smaller scale and was able to care for the rooting plants.
My main task throughout the week was aiding in data collection for a patented research project. I found the problem-solving aspect enjoyable and appreciated the opportunity to learn through trial and error, as well as develop more detail-oriented techniques for handling seedlings. It was exciting to see the results of my work from growing week to growing week and be able to document it. When it came to careers, I often thought about working in a research lab, but it was eye-opening to be able to experience this type of work at a production greenhouse. It made me realize there were many more opportunities to do the things I was interested in, outside of academia.
Tagawa Greenhouse is much more than a production facility, as they also merchandise their products at big box stores, as well as their own garden center. Being able to experience a many different aspects of the industry was one of the things that drew me to Tagawa. Not only was I able to work in production, but I was able to follow their plants from shipping and distribution right into stores, where I had the opportunity to interact with the public on the retail side of things, merchandise and set up displays of our plants, and learn from experienced master gardeners at Tagawa Gardens.
It was surprising how much I learned from my retail experience, having been a gardener myself for many years. I was able to see how the Tagawa name was synonymous with both quality and knowledge. Customers at retail chains knew that their plants came from Tagawa and would turn to the garden center for both more information and product. Every department at Tagawa Gardens had an expert in their area from whom I learned everything from how to prune a rose to how to help a customer find the right fertilizer for their needs and unique location.
Most years, Tagawa takes their interns to the ProGreen Expo, but due to Covid-19, the convention was online this year, but I was still given the time to attend the virtual panels and learn more about the green industry, the challenges of growing in Colorado, and new and developing greenhouse technology. I was able to watch lectures from CSU professors and see the type of research students were involved in at the university.
After I complete my associate degree in Horticulture, I had determined that I wanted to go on and continue my education at a state university and being able to see the work done at CSU added another school for me to consider if I decide to leave Iowa. Tagawa helped put me in contact with a professor at CSU who gave me a tour of their trial gardens and arboretum, as well as introduce me to their wonderful Horticulture program.
Interning at Tagawa Greenhouse was an amazing opportunity. It gave me a better sense of the type of work in horticulture I enjoy and showed me where I could apply my interests. There are more careers that I am now considering than I was prior to my internship, as well as more contacts to help me when I finally take my place in the industry or continue my education.
The six-month term was just long enough to see all sides of production and I wish I could have spent more time there, but I do have one more year to complete in my current educational program. My college was impressed with the internship program as well, and AFE allowed my instructor to visit and tour the facility. This fall, I will be talking to first-year students about my experiences at Tagawa and with AFE, encouraging more students to apply for the Vic & Margaret Ball Intern Scholarship. The distance was well worth the experience!
— Will Billmeyer
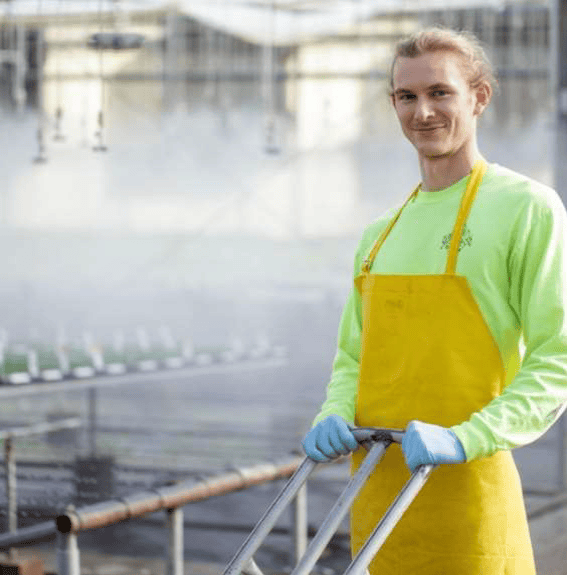
Sherman Hartman
2020 Intern
★ 2021 Paul Thomas Intern of Year
When I found out that I had received the opportunity to come to Colorado to study floriculture in Tagawa’s internship program, I was beyond excited. I wasn’t sure what I would get to see and take part in before entering the program. Having heard of this program and Tagawa’s reputation, I knew I would see some new areas within the greenhouse industry that I had not seen before, and also see some new species being grown in this production setting. It is safe to say that my expectations of this program were surpassed, despite COVID-19 and all. Even as an intern I felt I was a part of this special team here at Tagawa that truly does put people and relationships right up there with the plant quality.
I enjoyed the first rotation in operations for several reasons. It was exciting to be working with young, seemingly fragile cuttings and propagules at the Foothills location. I felt a bit like I was welcoming all of the boxes of cuttings into the facility and tucking them into the cooler before being stuck soon after. Later in that rotation I helped with a lot of sticking and jimmy-tagging. Following this order of receiving/unboxing cuttings, prepping for sticking, sticking cuttings, and finally pulling the finished trays to ship really gave me a sort of bird’s eye view to each order and tray, and how plant material arrives and finished orders leave the greenhouse with every step in between (besides the actual growing/production tasks). In this rotation, I learned the importance of organization whether it be good inventory practices to know where orders are being grown, or a good sticking line setup for efficiency.
Also, during this rotation I got to see first-hand just how versatile and flexible a greenhouse operation should be. From seeing management helping to fix sticking machines and tray filling equipment, to having employees switch over to hand sticking auto-stick cuttings in a pinch, this sort of versatility seems ingrained in this business dealing with live plants. That versatility was interesting to see in person; and was somewhat reinforced by the two-man teams constantly either building racks and moving around both empty racks and full racks of freshly stuck trays. It was those kinds of positions I had been overlooking in the industry, so it was great to take part in even if only briefly.
Following the operations rotation, I spend some time in production. I assisted in range D at the North facility, essentially as an irrigator but also helping out with and learning about other grower and general tasks too. I felt fairly confident in my irrigation abilities going into this rotation, but it turned out I got a chance to really focus that skill and others during my time there. It became utterly clear how important water quality is, and I assisted in testing our different water sources while the head grower was away for a couple weeks. I learned how to take into account dry down time, weather, fertilization needs, and general time management when planning out irrigations. Prior to this internship, I had tried to grow crops on the dry side with several small groups for assignments back in the campus greenhouse. After being shown the specifics and getting help fine tuning my irrigator’s judgment and watering hand, I found myself growing dryer more successfully and realizing that I never really had to a legitimate extent before. I got to see first-hand how certain cultural practices like moisture management and temperature from a plant’s early stages, can make all the difference in the final product of a nice full, toned plant.
One learning curve I was chasing for a short period of time was irrigating while taking into account the increasingly intense Colorado sun and heat during the spring months. Though I had a fair amount of moisture management experience in more humid climates, had never grown any plants in such an arid climate before being in production in range D. I believe it was mid-March when the temperatures and sun intensity began to rise beyond my anticipation leading to alarmingly fast dry down rates. I did not kill or really damage any plants during this time. Ashley instructed me to simply give more water to each container at each irrigation, and to walk my houses more frequently to ensure nothing gets too dry before I become aware of it. Even with that advice, it took me some time to adjust to these changing conditions. Nevertheless, this was an excellent learning opportunity for how one should take a wholistic approach to plant care, including weather directly influencing irrigation practices. I deeply enjoyed this rotation because of the responsibility that lies upon the irrigator, and how one’s knowledge and good judgement can keep a crop on track to finish beautifully.
In my retail ready rotation, I got to spend time at a Costco, several Home Depots, and at the Tagawa Garden Center. These venues are different in how they sell their plants, the kinds of plants sold and containers, and generally the sort of customers that shop at these different places. At the Costco, I noticed most everything was in large containers and in pre-arranged designs, though there were other crops like various herbs, tomatoes, peppers, and succulents, and some 12-packs. These customers seemed least interested in the involvement with the plants and would rather prefer a large container in full bloom ready to enjoy. The Home Depot selection was much wider, with many different species in various packs, small pots, hanging baskets, and also large containers. These customers seemed excited about buying packs of annuals to plant themselves either in containers of their own or in their flowerbeds. Many people would buy a wide variety of plants for their home as well as other gardening equipment from the Home Depot.
While working at the Tagawa garden center, there were a variety of different customers. Some customers didn’t know a petunia from a canna, and others had specific questions regarding different species’ preferences, plant care, and remedies for insects or diseases. This facility carried the widest variety of crops among all three retail locations with different sections for annuals, roses, vegetables, houseplants, perennials, and a nursery section. The garden center had so many different species that it seemed rare that a customer’s request could not be fulfilled. No matter who the customer was, it was fun to gauge peoples plant knowledge to be able to assist them accordingly. At the Costco and Home Depots, there generally seemed to be two groups of customers, those who buy a container because of how it looks right now, and those who buy it for how they anticipate the arrangement to perform throughout its life. I enjoyed helping customers at all of these locations, though the Garden center likely taught me the most, as they essentially have experts in each of the different areas mentioned above.
During the Coronavirus outbreak, the world seemed to be a completely new arena with potential infection lurking around every turn. Though it was surely frightening, especially in the beginning when nobody knew very much for certain, the central point of my focus of the Covid-19 outbreak here is not the fear it invoked, but rather Tagawa’s handling of it. Early on during late February and March, I thought that Tagawa might close down even if only temporary. This did not happen for several reasons. Firstly, this company falls under the umbrella of Agriculture. Also, serious precautions were taken at all Tagawa facilities in attempt to reduce the spread including mandatory masks and social distancing, and rigorous sanitation across all facilities. Though a few individuals within the company did test positive, sufficient precautions were taken so that the company was able to stay open and operate near full capacity throughout.
By mid-March, masks were deemed mandatory at all Tagawa facilities and interfacility travel was drastically reduced. At the same time, the maintenance employees found new tasks of walking around and spraying commonly touched surfaces with disinfectant. Bottles of disinfectant were never out of sight, and the head of maintenance even sent me home with a couple to keep the house as clean as possible. When Colorado instituted a stay at home order, all employees were given a document proving that they were essential employees at an essential business, in case anyone was stopped by police. Some rules even changed so that those who might have contracted the virus could receive more paid sick days to deter anyone who might have it from spreading it further within the company. Though the fear continues to linger about contracting the virus, Tagawa seemed to do everything in their power to keep all employees safe. Despite the fact that it was in Tagawa’s best interest to take every precaution possible, I am deeply grateful to have been with a company who cares about their employees’ safety during such a volatile time.
After having completed the internship program, I feel much more floriculture oriented in my career outlook. My time spent in the greenhouse and in all areas of this company have helped me to be much more prepared for any position I may enter, especially those within green industries. From here I will take all I have learned and most likely enter a greenhouse production position within the year following my college graduation. This may likely begin with an irrigator position or as part of a team performing general greenhouse labor. Another area of horticulture I am considering is nursery crop production. No matter where I end up, this program will have surely aided my professional and intellectual development to help me get there and with my performance in any such position.
Overall, I enjoyed my time in the Tagawa Greenhouse internship program very much so. I learned more in these last 6 months than I thought I ever could. I found great pleasure learning about aspects of the greenhouse industry that I was previously unaware of. The program is set up in a way that allows interns to get a feel for the seasonal nature of the industry, as well as the ability to gain work experience in many different aspects of this business’s inter-workings. To say I am grateful for this opportunity, and my time here would be an understatement and I would sincerely recommend this internship program to all horticulture students interested in floriculture.
—Sherman Hartman

Pearl Aragon
2020 Intern
The maintenance rotation was important because it showed me what it takes to maintain a greenhouse. I watched and participated in the flow of projects throughout the three days. I learned that a priority must be set in order to accomplish the maintenance and repair demands. Plans must be flexible, and staff training and experience is important. Having a good knowledge base, large skill set, and being creative is also necessary to complete a project. When replacing damaged polycarbonate panels on range A, Mario and Juan had to ensure they could make the repair without wasting the polycarb sheeting. A mistake in taking measurements or cutting the material equals a higher cost. I helped Mario with the cooling pad maintenance. We made sure the water output holes were clear and running down the cooling pad. Efficiently functioning cooling pads keeps the greenhouse from overheating and reduces water waste. I helped Juan paint the walls in range 3 and 4. Even though I ruined one pair of jeans and shoes, I had fun using the spray gun. I have never used one before. Juan did say he would never hire me to paint his house, which I can agree with. I guess I need more practice.
